Our XXL follow-up and assistance program is our state of the art advice and service program particularly interesting for container and tableware glass manufacturers knowing that....
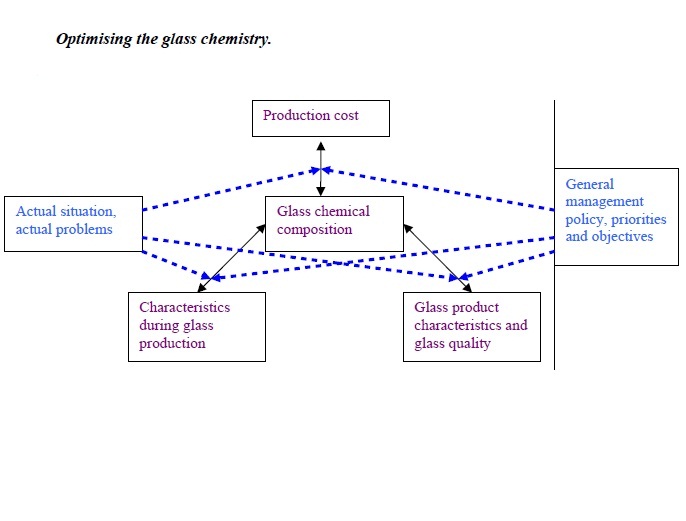
✔ External knowledge, experiences, new fresh ideas and new insights mostly result in long term important cost, quality and/or productivity benefits.
✔ Due to the complex interactions of all processes in glass manufacturing, efficiency and quality improvement opportunities are always present.
✔ Information and knowledge exchange and sharing new ideas with other companies is often difficult in this very competitive business.
✔ 100% independent glass technology advice and assistance is hard to find.
The objectives of our XXL glass technology follow-up and assistance program are:
➢ I. Production/operational cost reduction e.g. by minimising the glass batch cost, by decreasing the furnace energy consumption, ....
➢ II. Increasing the efficiency and productivity of the glass manufacturing process.
➢ III. Improvement of the overall glass quality and the glass products quality mainly by elimination as much as possible the sources for glass defects (in forming, in melting,..) and by improving quality control and quality assurance (procedures).
➢ IV. Assistance to the glass plant (technical) managers and operators consisting of training courses on specific topics and technical support (e.g. elaboration of calculations, procedures,...) according the needs in order to reach the above mentioned objectives.
Our XXL follow-up and assistance program consists of:
+ 'In the field' assistance, training and help at the glass plant.
+ A close continuous follow-up of the glass production data using (mainly) the internet for data and information exchange.
+ A monthly report containing all actual follow-up data, calculations, advice and (intermediate) project results.
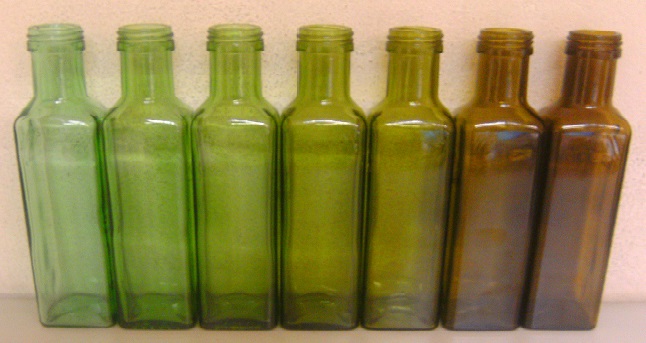
All major production processes are included in our XXL follow-up and assistance program:
• Raw materials, glass batch formula and glass chemistry:
◦ Raw materials selection, quality of raw materials, new raw material introductions.◦ Batch formula, glass composition and glass characteristics calculations.
◦ Optimisation of the glass characteristics e.g. viscosity, melting and fining characteristics, redox, chemical durability.
◦ Cost calculations and cost optimisation raw materials per ton molten glass.
◦ Glass colour improvements e.g. using physical and chemical decolourisation in flint glass, colour stability improvements, colour characteristics changes according (customer) needs.
◦ Optimised use of cullet (e.g. high cullet ratio batches), glass recycling, quality problems and quality control of cullet.
• Melting process and furnace operation and control:
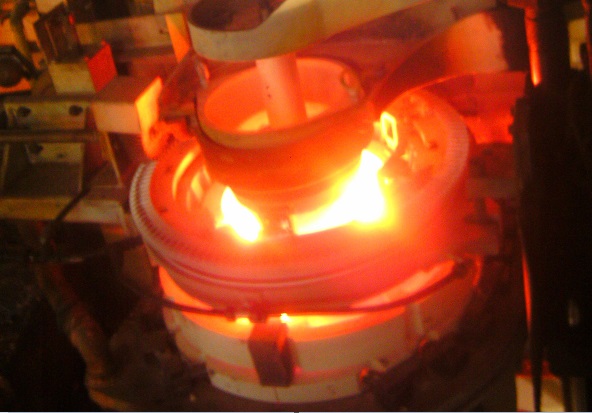
◦ Energy consumption reduction, energy balance calculations, check for abnormal energy losses, furnace performance benchmark.
◦ Optimisation and follow-up of furnace operation and control strategies (according pull, batch characteristics), combustion settings, glass flow pattern optimisation, ....
◦ Refractory corrosion, decrease of furnace refractory wear and chemical attack risk, furnace lifetime improvements.
◦(Re)fining process improvements, seeds and blisters reduction, solving reboil problems.
• Forming process:
◦ Feeder operation and control, temperature settings, ideal temperature profile.◦ Optimisation of glass characteristics in order to improve the forming process e.g. viscosity, working range optimisation, working point modification, ...
◦ Forming efficiency improvement e.g. by modification of forming-machine timing, gob temperature, feeder settings.
◦ Glass defects trouble-shooting.
◦ Coating process parameters, optimisation of coating, coating quality trouble-shooting.
◦ Temperature settings, optimisation of annealing process, annealing quality control.
◦ Glass products quality inspection improvement advice; optimisation elimination of critical, major and minor defects.
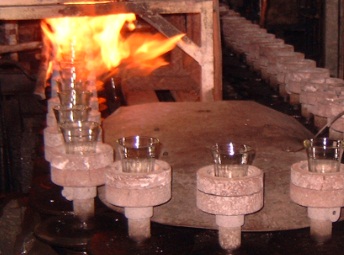
• Cold-end operation, inspection, glass quality control:
◦ Glass quality improvement; glass defects trouble-shooting.◦ On-line and off-line quality control procedures optimisation: statistical sampling review, on-line inspection, optimisation lab measurements, ....
◦ Optimisation of operating characteristics curve (producer's and consumer's risk); identification of quality assurance improvement opportunities.
All above mentioned items will be audited during the first visit at the beginning of the collaboration program. The extend of the further work for each item will depend on the actual possibilities and opportunities for improvement according the above mentioned major objectives (➢ I– III) and upon the objectives and priorities of the glass plant management.
Glass plant visits and assistance at the glass glass plant
In a typical XXL-program, four glass plant visits of (minimum) 5 working days are included:
– A first visit at the start of the project.
– A second visit during the first half of the project.
– A third visit during the second half of the project.
– A fourth visit at the end of the project.
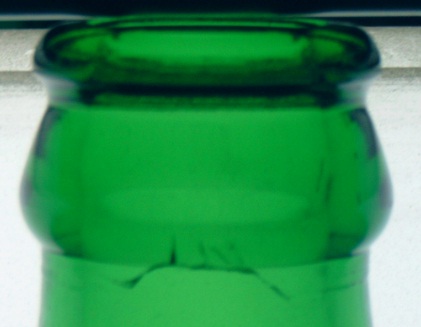
These visits will be planned according the specific needs and planning of the glass manufacturer, e.g. it may be more useful to plan a visit during a colour change or in a period with other major technical challenges.
• Typical objectives of the first visit are (indicative):
◦ To identify all opportunities and possibilities for improvement of each major production process according the main objectives of the project.
◦ To collect all important data on the production process and product quality.
◦ To elaborate an action plan in order to improve according the major objectives of the XXL program (➢ I - III).
◦ To set-up efficient communication lines between the glass plant and GEM-projects for project implementation and follow-up.
• Agenda and objectives of the second and the third visit are:
◦ To audit/review the whole production process and to determine the intermediate results and progress of the improvement program (compared to the results of the first visit/audit).
◦ To collect additional data, make observations and measurements, solve actual important problems (especially these issues where in the field observations are very important).
◦ To present the glass plant management the audit results, progress of the project, intermediate results and benefits (so far) of the project.
• A last visit will take place at the end of the project, including:
◦ A final audit and data collection.
◦ Detailed explanation of the results and conclusions of the project to the glass plant engineers and operators in order to assure the continuity of the benefits of this project.
◦ Presentation of the results of the improvement project to the management of the glass plant.
Monthly progress reports:
These monthly progress reports will contain info and data about e.g.:
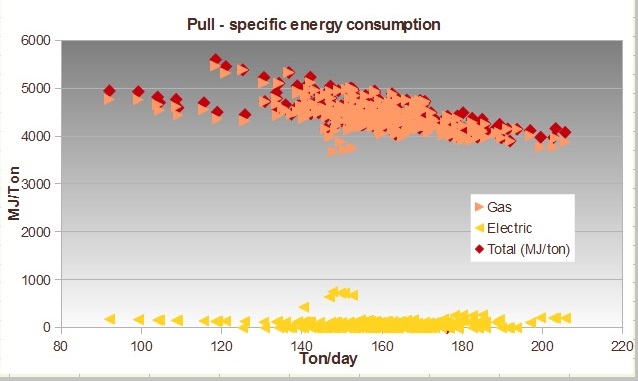
• The furnace performance, energy consumption, melting efficiency improvements.
• Glass forming efficiency, solutions to glass forming problems and defects.
• Glass quality and glass products quality improvement.
• Actual status and proceedings of the project.
• Technical explanations and help on important issues.
• Recommendations and action list for improvements according the main objectives of this project. Calculations and software, needed in order to reach the main objectives of this project (e.g. viscosity calculations, batch calculations, specific energy consumption monitoring, ...), that are missing at the glass plant will be programmed and implemented without any additional cost.
At the end of the project, a final project report will be made containing all data, calculations, technical explanations, actions, results and conclusions of the whole project.
Your major benefits:
• ✔+20 years of glass technology experience input and knowledge transfer.
• ✔100% independent review and audit and follow-up of the whole production process in order to for-fill the objectives of the project.
• ✔Highly valuable advice and help on all glass production and glass product problems and questions.
• ✔Plant visits and 'in the field' assistance without any additional cost for our work and services (excl. travel and hotel expenses).
• ✔Additional practical help, support and useful training courses about program issues like e.g. furnace control, glass chemistry included in the program,
• ✔as well as technical calculations (e.g. batch cost optimisation calculations, energy monitoring) and (for project implementation needed) glass technology software development.
• ✔Monthly project management reports with results of the follow-up, recommendations and project goals implementation.
• ✔Real measurable benefits on production cost reduction, productivity and quality improvement to your glass plant.
Interested in these benefits? Contact us for more info and/or an XXL collaboration offer.